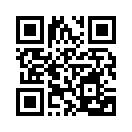
|
||||||||||||||||||||||||||||||||||||||||||
Полезные ссылкиМашина мозаично-шлифовальная Причины поломок шлифовальных машин по бетону Выход из строя мозаично-шлифовальной машины: вследствие неправильной эксплуатации является одной из самых частых причин убытков при использовании данного вида строительного оборудования. Агрегаты этого типа строители применяют для обработки бетонных поверхностей, которые уже набрали марочную прочность или покрытий с включениями натурального камня. Преимущества мозаично-шлифовальных машин с электрическим:Специалисты сходятся во мнении, что электромоторы в целом надежнее бензиновых силовых агрегатов. Операторы, работающие со строительной техникой данного типа, отмечают, что электрические моторы гораздо проще в обслуживании и менее прихотливы к внешним воздействиям. При проведении работ, электрические мозаично-шлифовальные машины меньше подвержены выходу из строя в случае возникновения непредвиденных ситуаций. Аварийные ситуации при эксплуатации мозаично-шлифовальных машин:Наиболее сложными случаями являются ситуации, когда сгорает двигатель. По каким причинам электромотор выходит из строя? Чаще всего это происходит не из-за перегрузок, как думают многие, кто незнаком с электрическими мозаично-шлифовальными машинами. Конечно, если заставить аппарат работать без перерывов, аварийная ситуация не заставит себя долго ждать. Но такие происшествия случаются достаточно редко – оператор понимает, что так работать нельзя. Гораздо чаще мозаично-шлифовальная машина выходит из строя в безобидной на первый взгляд ситуации. Питание поступает, двигатель гудит, но инструмент не шлифует поверхность. Характерной мелкой вибрации не ощущается. Неопытный оператор не сможет понять, что произошло на самом деле. На самых мощных моделях электрических мозаично-шлифовальных машин устанавливаются трехфазные двигатели. Если на питающей магистрали пропадает напряжение на одной фазе, двигатель не может работать. Неопытный работник не видит, что траверсы с алмазным инструментом не вращаются, и будет пытаться запустить аппарат, щелкая кнопкой выключателя. В результате обмотка двигателя сильно нагревается, изолирующее вещество расплавляется и выгорает. Вслед за этим происходит замыкание между витками проволоки – двигатель выходит из строя. Чтобы заменить сгоревшую обмотку, необходимо прибегнуть к услугам опытного моториста по электрическим двигателям. Другой распространенной причиной поломки двигателя является слабый контакт. Прерывающееся питание создает постоянные пусковые токи, которые ведут к сильному перегреву обмоток. В этом случае неопытный оператор может попытаться продолжать работать, решив, что рывки, подергивания и посторонние звуки вызваны какой-то другой причиной. Итог работы в таком режиме – сгоревший двигатель. Технологические этапы проведения работы Технологические этапы проведения работы по шлифовке бетона: Заливка бетона – сложный технологический процесс, в ходе которого раствор расслаивается, его крупные компоненты оседают вниз, а на поверхность выступает цементная жидкость, называющаяся молочком. Получается верхний слой очень слабым, что становится очевидным во время эксплуатации покрытия. На нем постоянно образуется слой пыли. А воздействие внешних факторов только усугубляет ситуацию, разрушая его. Поэтому встает вопрос об обязательном увеличении прочности верхнего слоя. Выход есть: шлифовка бетонного пола. К тому же этот процесс поможет выровнять верхний слой, сделав его идеальным. Как подобрать оборудование для выполнения работ?: Для выполнения этого процесса понадобится мозаично-шлифовальная машина. Это технологическое специализированное оборудование, которое производится сегодня исключительно для обрабатывания бетонных и природных покрытий. Мастерам обязательно понадобятся для работы фрезы. Масштаб процесса зависит от обрабатываемой площади. Имеет значение и ее конфигурация. В зависимости от этих параметров подбирается определенный вид мозаично-шлифовальных машин. Оборудование имеет различные технические характеристики. Они влияют непосредственно на время работ, связанных с обработкой бетонного основания. Вспомогательным оборудованием является промышленный пылесос. Он эффективно устраняет пыль с бетонной поверхности. Когда можно приступать к шлифовке бетона?: Оказывается, шлифовать бетонную поверхность нужно в определенное время. Нельзя приступать к работам сразу после того, как заливается бетонная стяжка. Ей нужно просохнуть. А значит, необходимо выждать неделю, а лучше всего – две. За этот срок бетон становится боле прочным и устойчивым перед обработкой алмазными фрезами. Технологические этапы шлифовального процесса: Вся работа состоит из нескольких этапов, технологию которых нужно знать в обязательном порядке. - Этап первый: Сначала подготавливается основание. Оно должно быть ровным, жестким и прочным. Для заливки пола используют бетон определенной марки, но не ниже М200. В бетонной основе не должно оставаться трещин и выбоин. Они тщательно заделываются. Когда ремонтно-восстановительные работы окончены, то сверху бетонное основание нужно обработать адгезионным грунтом. Это повлияет на повышение показателей прочности сцепления стяжки. - Этап второй: Укладывать бетонное основание нужно без остановок. Бетонный раствор разбавляется специальными добавками для улучшения эксплуатационных характеристик. Виброрейки выравнивают бетонную поверхность, удаляют из нее пузырьки воздуха. - Этап третий: К шлифовке нужно приступать только тогда, когда основание будет прочным. С поверхности удаляется выступающая цементная жидкость. - Этап четвертый: Бетонная поверхность обрабатывается пропитками. При этом не образуется эффект пленочного покрытия. На заметку: если планируются полировочные работы, то в таком случае рекомендовано проводить шлифовку бетонного основания. В саму смесь добавляется крошка природного происхождения. Это может быть гранитная или мраморная крошка. Отполированный и отшлифованный пол будет декоративно привлекательным. Советы по выбору алмазных франкфуртов и фрез Проясним ситуацию: если встала задача использовать мозаично шлифовальную машину, значит предварительные работы со свежим бетоном при помощи бетоноотделочных (затирочных) машин закончились неудачей (в лучшем случае остались небольшие огрехи). В отдельных случаях требуется придать поверхности визуальную привлекательность – отполировать бетон до зеркального блеска. В зависимости от площади и исходного качества бетонного покрытия подбирается зернистость расходного материала (франкфурты и фрезы алмазные). Начальное шлифование позволяет избавиться от неровностей пола высотой не более 1 см. При более значительных огрехах использование мозаично-шлифовальной машины нецелесообразно, необходимо применить фрезер по бетону. Как профессионалы мы советуем другой вариант: удалить неудавшееся покрытие с помощью отбойных молотков и залить бетон заново (часто данный способ обходится дешевле фрезерования). Начинать шлифование необходимо с максимально большого размера алмазного порошка: маркировка может быть как в размерах зерна, так и в количестве нулей (например, 800/500, он же просто 0). Следует учитывать, что производитель указывает ресурс франкфуртов и фрез алмазных в квадратных метрах при съеме 1 мм. Если требуется удалить 2 мм поверхности, заявленный ресурс уменьшается вдвое. Значительное влияние на расчет ресурса алмазного инструмента имеет возраст и марка бетона, коэффициент заполнения, который в связке с алмазным порошком может вести себя по-разному. Из-за большого количества влияющих факторов вычислить ресурс каких-либо франкфуртов или фрез практически невозможно. Очень большое значение имеет тип шлифования – сухой или влажный. При сухом типе алмазный инструмент расходуется быстрее, мокрый тип шлифования позволяет получить максимальный эффект при минимальных затратах. В некоторых случаях не рекомендуется использовать воду в рабочем процессе, поэтому приходится идти на повышенный расход ресурсов для соблюдения требований технологии. На качество работы большое влияние оказывает квалификация оператора. Более половины случаев неудачной работы обусловлены «человеческим фактором». Если работник не имеет практического навыка работы на мозаично шлифовальной машине, то результат почти наверняка окажется неудовлетворительным. Примерное количество франкфуртов и зернистость из расчета применения двухтраверсных машин типа Splitstone. Один комплект включает 3-6 штук. - при площади до 500 м2 можно использовать для начала размер зерна 1000/800 (00); - при площади более 500 м2 рациональнее использовать размер зерна 1600/1250 (000). Обработанный пол необходимо вымыть и осмотреть поверхность. Если пол недостаточно гладкий, требуется произвести вторичное шлифование алмазным инструментом зернистостью на ступень меньше примененной первично. Размер зерна 800/500 (0). Как правило, для простых полов этого бывает достаточно. Если необходимо добиться эффекта полированного пола, необходимо снижать размер зерна применяемого инструмента на ступень до достижения требуемого качества обработки поверхности. Выбор генератора Выбираем бензогенератор для сварочных работ Проведение монтажных работ методом дуговой сварки требует наличия надежного источника электрической энергии. В условиях строительной площадки предпочтительнее выглядит вариант с использованием бензинового генератора для сварочных работ, так как данный агрегат позволяет выполнять операции даже при отсутствии централизованного электроснабжения. Бензиновый сварочный генератор является электромеханической машиной, предназначенной для преобразования механического действия в электрическую энергию. Для сварочного инвертора необходимо использовать генератор с необходимой мощностью. Расчет мощности генератора для сварочных работ: Генератор подбирается исходя из параметров инвертора, и должен соответствовать следующим требованиям: - компактность; - мощность; - экономичность. Основным параметром, влияющим на ход трудового процесса, является мощность генерирующего электричество агрегата. Данному параметру необходимо уделять особое внимание при выборе генератора для электродуговой сварки. Рекомендуется брать бензогенератор превосходящий мощностью сварочный инвертор в два-три раза. Например, для стабильной работы инвертора мощностью 2,2 кВт требуется синхронный генератор от 4 кВт. При меньшей мощности генератор сгорит достаточно быстро, так как будет постоянно работать с полной нагрузкой. Стоит помнить, что чем меньше диаметр рабочего электрода, тем меньшая мощность требуется для осуществления процесса сварки. Существенное увеличение времени для сваривания деталей тонким электродом в частном строительстве не имеет особого негативного значения. Преимущества бензинового генератора: Бензогенератор для сварочных работ обладает неоспоримым преимуществом перед дизельным аналогом – выдает электроток более высокого качества. Отсутствие перепадов напряжения позволяет повысить комфортность трудового процесса и качество сварного соединения. Также плюсом использования бензинового агрегата является низкий уровень шума при работе. В условиях частного хозяйства и при проведении работ вблизи действующих общественных заведений бесшумность является весомым аргументом в пользу приобретения бензинового генератора для сварки. Не стоит забывать, что двухтактный двигатель не приспособлен к длительной работе, и может использоваться только для небольших работ в частном хозяйстве. Для более серьезной работы в коммерческих масштабах необходим генератор с четырехтактным двигателем. Виброинструмент Виброплита используется как оборудование, применяемое в дорожном строительстве. Она выполняет уплотнительную функцию, которая позволяет тщательно утрамбовать любой строительный материал, начиная от брусчатки, и заканчивая тротуарной плиткой, гравием, щебнем и песком. Часто, когда необходимо отремонтировать дорожное асфальтовое покрытие прибегают к использованию виброплиты. Потребительский рынок переполнен различными предложениями, находящимися в разной ценовой категории и характеризующимися технологическими преимуществами. Принцип работы устройств: Виброплиты в своем большинстве оснащаются чугунными площадками, или же выполненными из стали. Причем, ширина основания в данном случае будет иметь весомое значение. Поэтому, следует ориентироваться на ее размер, достигающий порядка 70 сантиметров. Оборудование работает на трех типах двигателей: бензиновом, дизельном, электрическом. Мотор, сотрудничая вместе с приводной муфтой, запускает в работу эксцентриковый вал. Именно таким способом и происходит вибрация площадки. Если рассматривать весь ассортимент подобной продукции, то нужно отметить, что вариант именно бензиновой виброплиты сегодня является наиболее популярным. Что же касается электрического оборудования, которое используется в стократ меньше, то оно не достаточно будет удобно для применения. Виброплита с дизельным двигателем стоит намного дороже. Поэтому потребитель и выбирает во многих случаях бензиновую продукцию, которая отличается простотой в эксплуатации, да и обслуживание обходится недорого. Если говорить про конкретные преимущества подвидов оборудования, то стоит заметить, что несмотря на дороговизну дизельного агрегата, устройства тяжелые по габаритам, но при этом намного экономичнее. Да и мощность их работы будет увеличена в разы. Кстати, такое оборудование больше востребовано в профессиональной сфере. На чем основан выбор виброплиты: Оборудование между собой разнится не только ценовой политикой и типом двигателя, но и способ передвижения может быть разным. Агрегат может быть прямоходным или реверсивным, способным передвигаться назад. последняя функция остается сегодня востребована для устройств более габаритных и тяжелых, которые фактически невозможно вручную развернуть или передвинуть. Дополнительно при выборе вибпроплиты обращаем внимание на: - то, из какого материала изготовлено основание оборудования (следует учитывать такой аспект, что подошва из стали подлежит довольно скорому износу); - имеет значение и ширина подошвы (чем больше она будет, тем более мощный двигатель будет работать в вибпроплите); - обращается внимание на размер транспортных колес; - наличие системы орошения порой является важной опцией, позволяющей качественно обработать асфальтовое покрытие; Выбор также должен ориентироваться и на массу виброплиты. Но в этом случае будет все зависеть от того, какого типа работу необходимо выполнить. Компрессорное оборудование Эксплуатация поршневых компрессоров Оборудование для нагнетания давления широко востребовано в самых разных областях промышленного производства. Находящийся под давлением в ресивере воздух имеет большую потенциальную энергию, поэтому эксплуатация поршневых компрессоров должна осуществляться с выполнением правил промышленной безопасности, охраны труда. Визуальный контроль технического состояния агрегата: Чтобы эксплуатация поршневых компрессоров была безопасной оператор должен оценить аппарат визуально на наличие повреждений. Большое внимание следует уделить осмотру кабеля, проверке его целостности, оценке состояния заземляющей шины. Следующий узел, который требует проверки, – ременная передача. Важно, чтобы ограждение было без повреждений, а ремни натянуты. Во время работы компрессора возникают амплитудные колебания, если аппарат не закреплен, вибрация может стать причиной выхода из строя подвижных деталей и узлов, поэтому оператору или другому ответственному лицу перед подключением агрегата важно убедиться в исправности опорных колес и системы амортизации. Каждый раз перед запуском компрессора необходимо проверять надежность соединения агрегата с воздушной магистралью. Также требуется проверить исправность аварийного клапана и автоматики управления. Обязательно нужно проверять уровень масла в картере поршневого блока. Работа без смазки гарантированно приведет к выходу оборудования из строя. Правильное подключение к электрической сети питания: Подключение компрессора к трехфазной сети осуществляется специалистом, который имеет соответствующую подготовку и допуск. Подсоединение кабеля к клеммам аппарата можно выполнять только при отключенной кнопке питания. После установления контакта мастер проверяет правильность подключения, включив и сразу выключив кнопку. Электродвигатель сделает несколько оборотов, и электрик проверит направление вращения шкива ременной передачи. Если вращение происходит в обратном направлении, необходимо поменять полярность подключения питающего кабеля. Порядок включения и выключения поршневого компрессора: Включенный аппарат некоторое время следует прогреть в режиме холостого хода. В течение 5-10 минут все движущиеся детали будут смазаны маслом, все это время выходной кран на ресивере должен быть открыт. После прогрева электрического двигателя и поршневого блока можно закрыть кран и нагнетать воздух в пневматическую магистраль. Промышленные аппараты оснащаются специальным регулятором степени компрессии. Остановка компрессора выполняется переведение выключателя в позицию «0» или OFF. Когда электромотор остановился, следует выпустить воздух из ресивера. Выбор компрессора для покраски Перед тем как выбрать, достаточно необходимым и важным фактом станет, оснащён нагнетатель автономной (топливной) или электрической передачей. Отличающий их показатель – мобильность агрегата. Автономные установки, работающие на бензине или же дизельном топливе, являются полностью мобильными и достаточно удобными при отсутствии источника электричества. Электропривод, в свою очередь, более экономичный в плане доступности источника питания, но при этом повсюду присутствует привязка к «шнуру». Также для качественной покраски необходимо правильно подбирать компрессор с хорошим краскопультом. Пневмокраскопульты собираются с использованием самых разнообразных технологий. Необходимо учитывать эту информацию перед тем, как выбрать установки, так как устройство подбирается, опираясь на производительность краскораспылителя. При неправильно подобранном агрегате, без учитывания необходимых параметров, вполне возможны, изменения рабочего давления из-за чего ощутимо упадёт добротность покраски. Помимо этого, лучше учитывать само рабочее давление. Стандартное рабочее сжатие компрессора ограничено до 8-10 атмосфер, набрав которые он автоматически отключается, а сигналом для включения стандартно составляет 6-8 атмосфер. Достигнув отметки в 6-8 атмосфер, компрессор запускается и восполняет объем недостающего воздуха. В покрасочных целях, практичней всего подбирать ресивер объёмом 100-200 литров. Также, нужен и приходиться к месту, блок аварийного отключения агрегата при перегрузках. Вычислив показатели параметров пистолета для покраски, а также ваших предпочтений относительно качества и оперативности, возможно, сделать заключительный выбор компрессора для покраски автомобиля. Множество отраслей деятельности задействуют уплотненный воздух в виде основного энергоносителя, имеющего обширные области применений. Конструируются компрессоры трёх классов: Бытовые компрессоры - их желательно выбрать для непостоянного применения, продолжительность безостановочной работы которых около 15-20 минут/час, а также применяемым рабочим давлением, не превышающим 8 атмосфер. Объем ресивера этого типа агрегатов изменяется от 6 до 100 литров, однако для безостановочной работы он абсолютно не годятся. Полупрофессиональные компрессоры - также непригодны для безостановочной работы, длительность использования ни в коем случае не должна быть более 40 минут/час, в тоже время подаваемое рабочее давление доходит до 10 атмосфер. Стандартный поставляемый объем ресивера от 50 до 500 литров. К основным же их преимуществам относятся простота самой конструкции и доступные цены. Чаще всего задействуют в работе мелких и средних производств, а также СТО, шиномонтажей и так далее. Профессиональные (промышленные) компрессоры – достаточно мощная промышленная аппаратура, применяемая чаще всего на больших предприятиях. Агрегат имеет огромные возможности и продуктивность, пригодный к продолжительной и напряженной работе. Объемы ресивера у этого компрессора от 25 литров. Замена клапана слива конденсата Эта статья о том, как недорого (около 70 руб.) и быстро (около 30 мин., если заранее подготовиться) заменить неудобный цилиндрический клапан слива конденсата на ресивере компрессора Ремеза СБ-4С-50. Если клапан от вашего компрессора потерялся, или просто кажется вам неудобным — эта статья для вас. Однажды, перед уходом домой, я открыл клапан слива. Через некоторое время заметил, что воздух выходит медленно. Решил повернуть его еще, а потом еще и еще. Затем щелчок и клапан исчез. Поиски продолжались около двух часов и сопровождались мыслями о том, что это непозволительная роскошь — искать столь простую деталь так долго. В итоге клапан не был найден, но созрел список требований к новому: ·Клапан должен быть удобным для откручивания(закручивания); ·Клапан не должен так легко и непринужденно теряться; ·Конструкция должна быть простой и недорогой. В качестве замены был приобретен клапан слива конденсата от GAV (28 руб.). С ушками, благодаря которым крутить его очень удобно. В одном из них мною было просверлено отверстие — клапан будет привязан и больше не потеряется. Часть первая: избавляемся от старого клапана Прежде чем вкрутить новый клапан, надо выкрутить старый. Греть резьбовое соединение не хотелось — чтобы не обгорела краска рядом. Были испробованы накидные и рожковые ключи, газовый ключ и даже небольшие тиски — остаток клапана никак не хотел сдаваться. Но перед правильно подобранным экстрактором и воротком он устоять не смог. Часть вторая: новый клапан И вот в ресивере красуется часть нового сливного клапана. Соединение уплотнено фум-лентой. Радостный момент: клапан уже может выполнять свою функцию. Остается одно «но». Он все еще может потеряться. Чтобы предотвратить это были приобретены(слева на право): ·трубочки для обжима поводка (15 руб.); ·рыболовный поводок из метллического тросика (1 метр, 3 руб.); ·вертлюги (25 руб.). Сначала монтируем клапан к тросику, через вертлюг. Затем — монтируем второй конец тросика к компрессору, вдали от вращающихся деталей. Заключение В ходе работ возникло две мысли: 1. Использовать леску. При толщине более 1мм она достаточно прочна, но проигрывает в технологических и эстетических свойствах. 2. Между вертлюгом и клапаном применить заводное кольцо. В окончательном варианте была реализована конструкция на заводном кольце: почувствуйте разницу! Автор: Александр, март 2010 Купили поршневой компрессор?, подводные камни! Вот Вы и купили компрессор! Что нужно сделать при начале эксплуатации нового компрессора После первых 8-ми часов работы. Необходимо проверить усилия затяжки болтов головок цилиндров поршневого блока . После первых 8-10 ч работы надо проверить и при необходимости подтянуть болты головок цилиндров поршневого блока, для компенсации температурной усадки. Несоблюдение данного пункта может привести к ремонту компрессора (замена прокладки головы) 1200-1800 руб/голова. Симптомы: голова качает в обратную сторону. После первых 50-ти часов работы. 1. Проверить усилия затяжки болтов головок цилиндров поршневого блока. 2. Проверить натяжение ремней После первых 50-ти часов работы и далее через каждые 300 ч работы проверьте и при необходимости отрегулируйте натяжение ремней, очистите их от загрязнений. При недостаточном натяжении происходит проскальзывание ремней, возникает вибрация с воздействием на подшипники знакопеременной нагрузки "продергивание", перегрев шкивов, перегрев и снижение КПД блока поршневого. Когда ремни перетянуты, то происходит чрезмерная нагрузка на подшипники с повышенным их износом, перегревом электродвигателя и блока поршневого. После первых 100-та часов работы. После первых 100 часов работы необходимо провести замену масла. Далее через каждые 300 часов работы нужно также менять масло. Для заправки компрессора рекомендуется использовать компрессорные масла. Не следует использовать для поршневых компрессоров масло, предназначенное для пневмоинструмента или масло для винтовых компрессоров. Автор: KratonShop, апрель 2015
|
||||||||||||||||||||||||||||||||||||||||||
|